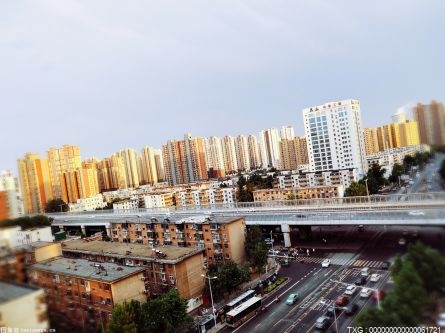
身为工程师应该都有过这样的经历吧,辛苦完成项目板子如释重负,送去打样,样品出来,一夜回到解放前。
板子具体的问题,有的是设计的问题,有的是生产制造的问题。当然有很多问题都可以在生产制造前给避免掉。
这里介绍在PCB生产制造前可以避免的22个PCB设计错误,帮你构建高效制造且无缺陷的PCB。
(资料图片仅供参考)
这里主要分为 2 个部分:1、PCB 可制造性设计
不完整和无效的设计文件
基材材料不当
走线宽度不当
走线间距不当
酸性陷阱
迹线或者钻孔到边缘的间距不足
钻孔过程错误
环形圈的缺陷
阻焊层错误
铜和阻焊条
散热器-多余的热量
丝网印刷错误
2、面向装配的PCB设计
数据效率低下
选择错误的组件
组件可用性
足迹不正确
元件间距不足
组件到边缘的间距不足
焊盘尺寸和间距不正确
丝印错误
高温误差
PCB 可制造性设计
可制造性设计 (DFM) 是一套用于识别电路板中可能存在的错误的指南。在设计阶段纠正这些问题可以使电路板生产更有效率,并避免生产过程中的任何延误。通常,每个制造商都有一个他们自己的独特的 DFM 清单。
一、不完整和无效的设计文件
无论是 Gerber 还是 ODB++亦或者是BOM文件,输入文件都包含重要信息,例如层图像、物料清单、电路板轮廓、IPC 网表、主图纸和层顺序。
规范中的任何混淆都可能在后期阶段产生问题。因此,在提交生产之前检查所有强制性文件。下面列举了一个DFM 工具所要求的 Gerber 文件和 BOM 文件的格式。
设计文件格式
设计文件格式
二、基材材料不当
一些电路根据其功能需要特殊材料。例如,典型的基板不能很好地处理高频信号。这里就需要制造商讨论材料要求,并在初始阶段选择合适的 PCB 基板材料。
三、走线宽度不当
铜迹线连接电路中的所有组件。迹线中的任何缺陷都可能导致短路、信号失真和散热。导体(迹线)的载流能力随其宽度的增加而增加。
如果更高的电流流过线路,则散发的热量会更多,从而导致电路板过热。因此,根据你的电路要求优化导体宽度,并确保外层走线宽度保持在 4 mil 以上。
你可以使用在线工具进行优化走线宽度、电流容量和温升。
四、走线间距不当
确保不要为了使电路布局更紧凑而牺牲导体间距,走线间距太小会导致闪络和串扰。
你应该遵循标准指南并在导体之间提供足够的间隙,与走线宽度一样,你可以使用导体间距和电压计算器计算导体之间的最佳间距。
走线间距
五、酸性陷阱
在走线布线过程中,如果任何一条线形成锐角(低于 90°),就会形成酸阱。在蚀刻过程中,残留的酸会被困在弯曲区域,这会导致走线的过度蚀刻。
如下图所示,通过在布线时防止锐角弯曲来避免酸陷阱。
酸陷阱形成
六、迹线或者钻孔到边缘的间距不足
你应该在电路布局中保持边缘和走线之间的最佳间距。如果你因为一些原因减少空间,那么在去金属化过程中,外部导体可能会被部分剃掉或者切割。
铜和电路板边缘之间的间距不足会导致铜裸露和边缘出现毛刺。
钻孔到边缘的距离
七、钻孔过程错误
在印刷电路板中,制造商会为各种目的钻孔,例如过孔、对齐、元件放置等。钻孔是一个不可逆的过程,任何不需要的钻孔都可能让你的设计功亏一篑。
其他需要考虑的因素是尺寸、间距、纵横比、板上的孔数和机器类型(激光/机械)。
影响钻孔的常见错误是孔环和钻孔到铜的距离不足。
钻孔规范
八、环形圈的缺陷
环形环将通孔连接到迹线,如果环形圈的直径不足,它将断开导体和过孔之间的信号流。
完成的钻孔可能有 ±2 密耳的公差,因此当小于 2 密耳时,环形圈可能会出现破裂。这会导致开路。
除此之外,元件孔的环形圈不足会导致组装后焊点不良。
环形环放置
九、阻焊层错误
PCB 上的阻焊层可保护表面免受污染并隔离连接。制造商在焊接过程中揭露放置元件的区域(足迹和焊盘)。
如果通孔掩模开口与相邻元件开口之间没有适当的间隙,则可能会在组装过程中形成焊桥,这会导致焊点不良且效率低下。
因此,必须在通孔开口和相邻元件开口之间保持所需的阻焊层。
焊桥的 CAM 快照
另一方面,不适当的阻焊层会导致形成焊孔,暴露的铜容易受到腐蚀。
十、铜和阻焊条
铜条是在印刷阶段形成的松散结合的薄残留铜段,在电镀过程中,这些松散连接的细长条会脱落并落入电镀液中。
这些光刻胶碎片可以共同沉积在电路板上的任何地方,从而导致短路。与此同时,去除光刻胶的区域会导致电路板上出现不需要的铜,这可能会影响电路板的功能。
铜条风险
阻焊层的成像过程中会形成阻焊条,在阻焊层处保留阻焊层以避免焊料桥接。
当水坝小于 4 密尔时,这些松散结合的水坝有可能变成条子并在开发阶段被冲走。
阻焊层条风险
十二、散热器
焊接过程会产生过多的热量,可能会损坏电路板。为避免这种情况,你必须提供足够的散热衬垫。
导热垫由称为“热量”的小铜辐条组成,以帮助导热。
如果这些热量与焊盘或平面断开连接,则它们被称为饥饿热量。这些热量不足会导致导热性差并使电路板过热。
十三、丝网印刷错误
丝网印刷是在制造过程的后期进行的。印刷时,如果丝印重叠在焊盘、PCB 表面、孔等处,可能会在组装过程中产生问题。
例如,如果丝网印刷在焊盘上,它会熔化到焊点中并产生不连续性。
面向装配的 PCB 设计
装配设计 (DFA) 过程缩小了设计师的愿景与生产过程的现实之间的差距。
你需要检查组件可用性和位置,了解DFA可以帮你简化 PCB布局以降低项目的总体成本并降低设计失败的概率
以下是 PCB 设计中一些最常见的 DFA 错误:
十四、数据效率低下
与 DFM 类似,你应该在设计进入装配过程之前验证所有基本数据表验证关键参数,如封装尺寸、XY 数据、DNI 规格、SI 数据、零件编号等。这样的话,可以避免之后的更正和确认。
验证关键参数
十五、选择错误的组件
零件的选择会影响装配过程。例如,与表面贴装技术 (SMT)相比,通孔元件需要复杂的制造工艺。因此,最好只在需要时使用它们。
始终选择标准组件而不是自定义组件,因为标准元素很容易从多个供应商处获得。由于你只能从选定的供应商处采购定制零件,因此它们通常不适合大批量生产,而且还会增加成本。
提供不同类型的组件
十六、组件可用性
在构建物料清单 (BOM) 之前,应该始终确认部件的可用性。如果供应短缺,你应该准备好使用来自不同供应商的替代组件。目前市面上也有很多BOM物料查询的网站,如下图,会提供物料,以及缺货等提示。
图片来源于findIC
十七、物件封装不正确
BOM 指定组装电路板所需的所有组件。如果 BOM 中指定的组件尺寸与CAD封装数据不匹配,则将很难完成电路。这将对自动化装配线造成重大困难。
纠正这种情况将很费时,也会增加成本。因此,请在设计阶段仔细检查组件尺寸。
十八、元件间距不足
在元件放置过程中,间距不足会导致零件重叠、形成焊桥等。在零件之间提供足够的间隙也有利于手动焊接和返工。特别注意 QFP/QFN、POP 或 BGA 等敏感元件的间距。
有时,元素会紧密放置以实现更小的外形尺寸。最好遵循间距指南,以确保零件间距零误差。
下图显示了 PCB 上的首选组件布局。
PCB 上的首选组件布局
十九、组件到边缘的间距不足
完成组装过程后,面板将经过分板过程。在此过程中,电路板末端的部件将不得不承受可能损坏它们的高应力。因此,在组件和边缘之间提供足够的间距。此外,间距选项因不同的装配工艺而异。
与自动组装相比,在手动组装中,你可以将单元放置得更靠近边缘。
标准组件到边缘间距
二十、焊盘尺寸和间距不正确
选择较小的焊盘尺寸会在 SMT 元件中产生较差的焊点,甚至在应用于通孔部件时可能会断裂。
使焊盘尺寸尽可能大可能不是解决方案。较大宽度的焊盘会占用更多空间,并且会使 SMT 元件在焊接时从其位置移动。
与焊盘尺寸类似,焊盘间距不能太近或太远,因为它们在放置元件时会造成问题。
二十一、丝印错误
丝印层包含许多重要信息。一些示例是元件方向标记、引脚 1 标记、极性标记、阴极标记等。
如果这些细节缺失或不清楚,那么装配厂将浪费时间来确认正确的数据。
在最坏的情况下,如果丝网印错了极化等数据,组装人员相应地安装了元件,那么电路板可能会出现故障。你需要在组装开始前确保丝印的可读性良好。
二十二、高温误差
制造商在焊接过程中需要适当小心,因为它会产生过多的热量,从而损坏电路板。控制此过程中产生的热量至关重要。提供足够的导热垫以有效散热。
DFM和DFA 指南可以帮你规避掉一些PCB设计问题,可以将设计错误的影响降至最低。
目前市面上还是有一些DFM设计工具的,我自己也有试用到一些还不错的工具。大家可以自己去选择。
以上就是关于 22种PCB设计错误,希望大家多多支持。
来源:头条号百芯说DFM
审核编辑:汤梓红
标签: